品質管理とは?生産管理との違いや基本的な業務内容、手法も解説
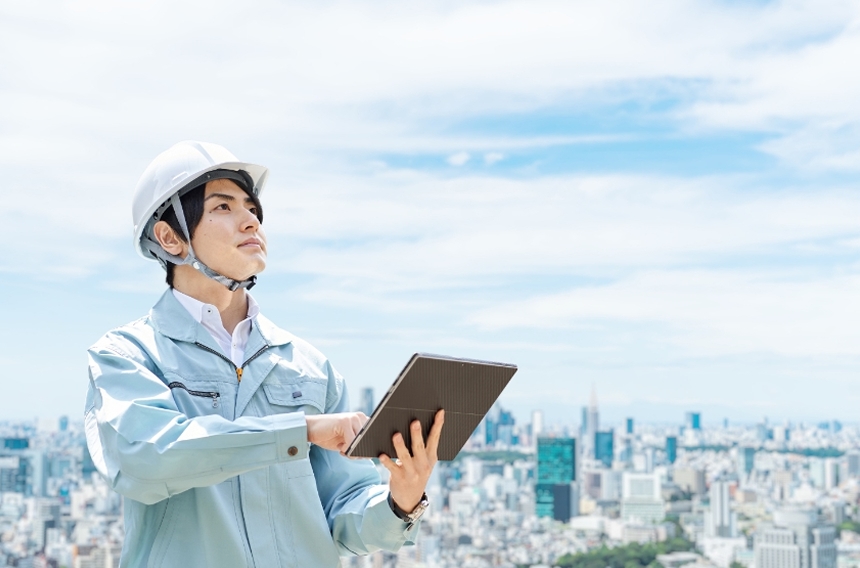
Check!
- 品質管理とは、商品の製造・提供にあたって一定の品質を保っているか管理すること
- 品質管理の基本業務には、工程管理・品質検証・品質改善がある
- 品質管理には「PDCAサイクル」「QC7つ道具」「IE」「5S」「4M」などの手法がある
品質管理とは商品の製造・提供にあたって一定の品質を保っているか管理することで、「QC(Quality Control)」とも呼ばれています。基本業務には工程管理・品質検証・品質改善が含まれます。この記事では、品質管理の仕事内容や手法などについて詳しく解説します。
おすすめ記事
品質管理とは

品質管理(Quality Control)は英語表記を略してQCと呼ばれることもあり、製品の生産工程において一定の品質を保つように管理する取り組みのことをいいます。不良品をなくして企業の信頼を保つために欠かせない管理です。
日本企業は従来から高品質な製品を作り続けてきました。しかし、少子高齢化による働き手不足などで、品質低下が危惧されています。そのような中で、高品質な製品を製造し続けるために、徹底した品質管理を効率的に行うことが企業の大きな課題になっています。
しかし、高品質な製品を追求して、過大なコストがかかっては企業の収益にはつながりません。品質管理はコストを抑えながら、顧客が求める品質以上の品質管理を行い、納期を守って完成させることが求められます。
品質管理には手間がかかります。しかし、顧客満足度の向上や業務効率化・コストの削減にもつながり、結果的に企業の信頼と収益の向上につながる重要な業務です。品質管理とよく似た言葉で生産管理や品質保証がありますので、以下でこれらとの違いを解説します。
\気になる項目をクリックで詳細へジャンプ/
生産管理との違い
生産管理とは、需要を予測して製品を製造するための資材調達から生産手順の調整・在庫管理・納入管理までの業務全般を管理することです。その目的は、一定の品質を保って、限られたコストで納期までに生産できるように生産活動を管理することです。
したがって、品質管理は生産管理の中の一定の品質を保つ部分を担う業務といえます。実際に行う際には、コストの抑制と品質の向上が求められるので、品質管理と生産管理は複雑に絡み合うため、品質管理と生産管理の境目は不明瞭です。
品質保証との違い
品質保証とは、完成した製品が定められた品質を満たしているかを確認する取り組みで、基本的には顧客の満足度に視点を置いた業務です。業務としては、顧客の感想やクレームなどの分析を関係部署にフィードバックし、顧客満足度の高い製品を目指します。
一方、品質管理は資材調達・製造・在庫管理などの業務の中で行います。したがって、品質管理は企業が製造工程全体で品質を見直していく業務なのに対して、品質保証は完成した製品の品質を顧客目線で見直していく業務であるという違いがあります。
検査との違い
検査とは、製品がきちんと品質の基準を満たしているかを確認することです。検査体制を強化することにより、不良品の流出を防ぎつつコストも削減できます。また、製品の問題を早期に発見し、市場での信頼失墜やリコールなどのリスクを軽減できます。
一方品質管理は、顧客の求めている良い製品をどのように作るかなどの方法を考えることです。つまり、品質管理は顧客満足と製品の信頼性向上を目指す総合的なプロセスに対し、検査はそのプロセスの中で具体的な品質に関する確認のための機能と言えます。
品質管理の基本業務

品質管理の基本的な業務は、工程管理・品質検証・品質改善です。ここでは、その3つの業務について詳しく解説します。
\気になる項目をクリックで詳細へジャンプ/
工程管理
工程管理とは、製品の資材調達から製造工程までの管理で、一定の品質を保ちながら効率的に製造が進むようにする業務です。また、コスト削減や設備維持・従業員の育成にもかかわります。
工程管理の主な業務は「作業手順の標準化」「品質教育と作業訓練」「設備の維持管理」「工程を正常に保つ管理」の4つです。
「作業手順の標準化」とは、誰が製造しても同じ品質が保てるように、製造手順の統一化を図る業務です。手順をマニュアル化し、従業員がそれに沿って作業をするなどして、いつでも・どこでも・誰がやっても同一品質の製品が製造できるようにします。
「品質教育と作業訓練」は、品質を保つための人材育成を行う業務です。品質保持の知識を身に着けるための研修や、現場で上司や先輩が技術指導を行うOJTなどがよく行われます。同時にマニュアルの周知徹底も重要な業務です。
「設備の維持管理」とは、日常の設備点検を充実させ、設備の不良による品質の低下を防ぐ業務です。日常的に点検・調整・修復を行えば、常に最適な設備で一定の品質を保った製品の製造ができます。
「工程を正常に保つ管理」は、工程を確実に進め、工程の中のミスを防いで製品の品質を保つ業務です。工程を正常に保つ管理では、工程の可視化が重要で、それぞれの工程が持つ特性や管理方法などを記載したQC工程表などがよく利用されます。
品質検証
品質検証とは、完成品だけでなく原材料や部品などの生産工程を検査する業務で、主に「製品品質の検査」と「工程能力・管理状態の監視」の2つがあります。
「製品品質の検査」は、製造のために調達した原材料や部品が要求した品質を満たしているか、また完成した製品が顧客の要求する品質を満たしているかの検査を行います。製品によっては、製造途中で検査を行う場合もあります。
「工程能力・管理状態の監視」は、製造工程が品質を保つのに適切であるかを監視します。工程能力を数値化した「Cp」や「Cpk」などの工程能力指数がよく用いられます。管理状態の監視では、管理の適正を監査などで監視します。
品質改善
品質改善は、不適合な製品が出た場合に原因を突き止め、再発防止策や未然防止を行う業務です。再発防止は、現状の把握→原因の分析→対策立案などの「問題解決ストーリー」と呼ばれる一連のステップに基づいて行うのが一般的です。
また、未然防止では製造工程に潜在する故障やトラブルをあらかじめ洗い出して取り除きます。未然防止のためのFMEAの考え方を製造工程管理に応用した工程FMEAを用いるのが一般的です。工程FMEAの対象は、材料・設備・人・方法・計測などに渡ります。
品質管理に関連する規格・資格

幅広い業務を担う品質管理には、さまざまな資格があります。ここでは、企業が取得するSO9001と個人の資格であるQC検定について解説します。
\気になる項目をクリックで詳細へジャンプ/
ISO9001
ISOは国際標準化機構と呼ばれるスイスのジュネーブに本部を置く非政府機関で、国際的に通用する規格の制定を行っています。ISO9001は、品質マネジメントシステム規格と呼ばれているISOが制定した国際規格の中の1つで、最終目的は顧客満足度の向上です。
また、品質だけでなく、価格や納期のバランスも重視されます。ISO9001取得には、高品質な製品を提供するプロセスを継続的に改善する仕組みの構築が必要で、多くの要求事項を満たさなくてはなりません。
ISO9001の取得は、取引先からの求めで取得する場合もありますが、公共工事の入札加点になっているなど、受注に有利な面もあります。さらに、業務効率化や社内の意識改革など、企業の内部改革に利用される場合もあります。
参考:概要 | ISO 9001(品質) | ISO認証 | 日本品質保証機構(JQA)
QC検定
QC検定は日本品質管理学会の認定を受けた日本規格協会が行う検定で、製品やサービスの品質管理に関する知識を評価する民間資格です。品質管理検定とも呼ばれています。検定は1級から4級まで筆記試験で行われ、どの級からの受験も可能です。
各級取得の対象者の概略は以下のようになっています。
- 4級:これから企業で働く方
- 3級:QCの7つ道具などの手法を理解している方
- 2級:QCの7つ道具などを使って品質にかかわる問題解決を求められる方
- 1級・準1級:品質管理全般についての知識が要求される業務に携わる方
詳しくは下記の参考資料に示されています。
参考:QC検定 | 日本規格協会 JSA Group Webdesk
品質管理の手法

品質管理には多くの手法やそれぞれに適したシーンがあり、必要に応じて使い分ける必要があります。ここでは、その中でも代表的な手法を解説します。
\気になる項目をクリックで詳細へジャンプ/
PDCAサイクル
PDCAとは、計画(Plan)・実施(Do)・評価(Check)・改善(Action)という4つのプロセスの頭文字を取った品質管理方法です。この4つのプロセスを繰り返すことで、継続的な品質改善を行うのがPDCAサイクルです。
Planでは品質管理の問題点を洗い出し、それを解決するための計画と数値目標を設定します。DoではPlanで立てた計画に沿って、後から分析・評価しやすいようにタスクを細分化して実行・記録します。
Checkでは目標数値の達成具合を細かく分析・評価します。目標数値の達成にかかわらず、その数値が出た原因をDoの結果から見つけます。ActionではCheckで発見された課題から、継続すべき点と改善を要する点を探ります。
QC7つ道具
QC7つ道具とは、製品の製造工程や品質にかかわる数値データを統計的に分析して、品質管理を行う7つの手法のことです。ここでは、それぞれの手法について解説します。
1. グラフ
グラフは、データの視覚化のために大変有効な手法です。品質管理によく使われるグラフには、変動を見る折れ線グラフ・数量を比較する棒グラフ・比率を見る円グラフ・比率を比較する帯グラフ・バランスを見るレーダーチャートなどがあります。
目的に合ったグラフを正しく利用することが重要です。たとえば、時間ごとの不良品の発生数を知りたいなら、時間と不良品数を軸に取った棒グラフの利用が適切です。また、同じデータでも何種類かのグラフに描くと、違った課題が見えてくることも多いです。
2. チェックシート
チェックシート(Check Sheet)は点検・記録のためのシートで、あらかじめ必要なチェック項目を洗い出し、それに沿ってチェックをすることで、品質の低下を防ぎます。日々のチェック用や定期検査用のチェックシートが作成されている場合が多いです。
決められたチェック項目で点検していくので、チェック漏れやデータの収集忘れなどを防げます。しかし、チェック項目の検討は慎重に行う必要があり、必要に応じてアップデートを繰り返し、より精度の高いチェックシートにしていく必要があります。
3. パレート図
パレート図(Pareto Chart)は、「全体の数値の80%は、全体を構成するうちの20%の要素が生み出している」とした、パレードの法則に基づいた分析方法です。品質管理では不良品の原因を発見し、優先すべき改善は何かを特定するために使われます。
作成では、不良具合項目別に件数を出し、件数の多い項目順に棒グラフを並べ、各項目の累積比率の折れ線グラフを重ねます。すると、大きな影響を与えている項目が明確になり、改善すべき点が特定されます。また、改善後と比較すればその効果の確認も可能です。
4. ヒストグラム
ヒストグラム(Histogram)は度数分布図とも呼ばれ、データを何らかの区分ごとに集計して棒グラフを並べたものです。データがどのような値を中心にして、どのようなばらつき方をしているかを可視化して把握する手法です。
品質管理では、製品過程で出る寸法・回転数・抵抗値などのばらつきの状態が把握でき、改善策の絞り込みがしやすくなります。グラフの山が規定値で最も高く、幅が狭いグラフになるのが理想で、それに近づけるような品質管理が必要となります。
5. 特性要因図
特性要因図は、図が完成すると魚の骨のような形になることからフィッシュボーン図とも呼ばれています。発生した課題や問題が起こった要因をあぶり出すために用いられる手法です。
魚の背骨に当たる部分に解決したい課題や問題点の矢印を描き、思いつく要因を背骨から出る大骨のように描きます。そして、大骨になる要因を生じさせている細かな要素を大骨から出る小骨のように描きます。それを繰り返しながら、解決すべき要因を洗い出します。
さまざまな要因の洗い出しには、4Mの手法が役立ちます。特性要因図を作成することで、先入観のない冷静な原因追及が可能になり、思いもよらない課題の発見に役立つことも多いです。
6. 散布図
散布図(Scattered Diagram)は、2つのデータの関連性を調べるために用いる手法です。関連性を調べたい2種類のデータを縦軸と横軸に取り、点をプロットしていく方法で、製造現場では、製造条件と不良率・厚さと耐久性など2つの関連性を調べるのに用いられます。
一般的には、点の集合が右上がりの直線状に並べば2つの相関が強く、満遍なく散らばる場合は相関が薄いと判断できます。相関関係を数値的に表したものが相関係数で、相関係数が 1または-1に近いほど強い相関があり、0に近いほど相関が薄いといえます。
7. 管理図
管理図(Quality Control Chart)とは、品質のバラつきが規定値内に収まっているかの判断のために用いられるグラフです。管理図は、中心線(平均値)・上方管理限界線(UCL)・下方管理限界線(LCL)の3つの要素から構成されています。
3つの要素と各条件の品質データを折れ線で表したものが管理図で、品質が安定していれば中心線と折れ線がほぼ一致し、品質にばらつきがあると中心線を上下した折れ線になります。管理限界内であれば許される範囲ですが、将来的に問題が発生する可能性があります。
IE
IE(Industrial Engineering)とは、生産工学または産業工学とも呼ばれる、製作工程を科学的に分析する手法で、無理・無駄・ムラを省いた製作工程の最適化を目的としています。品質管理を始めとする企業経営全体の改善に用いられる多様性のある手法です。
IEには数多くの手法があり、それぞれの基礎となっているのがワークスタディと呼ばれる作業研究です。そして作業研究は、さらに「方法研究」と「作業測定」の2種類に分類されます。下にこの2つの概要を示しておきます。
分類 | 概要 |
---|---|
方法研究 | 作業工程・作業方法・作業動作を系統的に分析することで、無理・無駄・ムラを発見し改善を図る(工程分析・動作分析) |
作業測定 | 各作業を定量的に測定し、非効率な作業を削減して生産的作業の標準時間を設定する(稼働分析・時間分析) |
5S
5Sとは、整理(Seiri)・整頓(Seiton)・清掃(Seisou)・清潔(Seiketsu)・躾(Shitsuke)のことで、それらの英語表記の頭文字を取って5Sと呼ばれています。日本独特の企業改善のための基本活動で、製品製造の品質管理にもかかわってきます。
組織としての業務の無駄・無理・ムラをなくすことが5Sの目的です。企業改善や品質改善にはコストがかかるのが一般的ですが、5Sはコストをかけずに誰でも簡単に取り組めることが最大のメリットです。
項目 | 概要 |
---|---|
整理 | 必要なものと不必要なものに分けて、不必要なものを処分する |
整頓 | 必要なものを定位置に置き、誰もがいつでも取り出しやすくする |
清掃 | 作業場や機器・機材を掃除をし、常にきれいな状態を立つ |
清潔 | 整理・整頓・清掃を保つ活動を行い、よい状態を継続的に維持する |
しつけ | 定められたルールや手順で業務を行う習慣づけをする |
4M
4Mとは、人(Man)・機械(Machine)・材料(Material)・方法(Method)のことで、それらの英語表記の頭文字を取って4Mと呼ばれています。4Mは、品質管理業務に欠かせない要素で、4Mを適正化することで高品質の製品の製造が可能になります。
4Mの目的は、製品の品質を向上させ顧客満足度を高めることで、そのほかにも製造コストの削減・生産性の向上・安全性の向上など多くの効果が期待できます。以下に4Mで行うべきことを簡単にまとめておきます。
項目 | 概要 |
---|---|
Man(人) | 適切な人材配置・効率化した作業方法の確立・業務に必要なスキルアップなどを行う |
Machine(機械) | 点検やメンテナンスによる、故障やエラーの予防や早期発見で、常に品質を保つ |
Material(材料) | 仕入れる材料や部品の規格検査の実施や、仕入先・調達手段・運搬方法の見直しを行う |
Method(方法) | 効率のよい作業方法を確立し、マニュアルや作業指示書による作業や資材調達の徹底を行う |
TQC
TQC(Total Quality Control)は、全社的品質管理とも呼ばれる、品質を総合的に管理するための手法です。TQCでは、組織の全員が全ての工程において品質向上活動を行い、常に品質改善を追及する姿勢が必要です。
TQCは1990年頃までは多くの企業で広く用いられた手法ですが、グローバル化やシステム化への対応への弱さがあり、現在ではTQCの中でも現代に通用する面だけの適用となっています。しかし、問題解決や品質改善の面においてはすばらしい手法と言えます。
TQM
TQM(Total Quality Management)は総合的品質管理とも呼ばれ、TQCを現代に対応するように改良したものです。2つの大きな違いは、TQCは組織全員で行うボトムアップの品質管理なのに対し、TQMはトップダウンで行う品質質管理となっています。
TQMとは、開発から製造・出荷まで全社員が品質改善の意識を共有し、継続的に品質改善に取り組むためのマネジメント手法です。そのため、PDCAサイクルなどを用いながら、社員教育や訓練・組織改善・顧客ニーズの把握などの幅広い取り組みが必要となります。
SQC
SQC(Statistical Quality Control)は統計的品質管理とも呼ばれ、収集したデータの分析によって品質管理や生産工程の改善を行う手法で、品質のばらつきを抑えるのが目的です。
品質差の要因は、材料・機械装置・作業方法・検査方法のどこかにあり、それらを適正化すれば品質の均一化が図れます。したがって、それらの要因のさまざまなデータを収集し統計的手法で分析することで、品質に差が起こる要因を追求して改善に結びつけていきます。
生産管理システムで品質管理を効率化

生産管理システムは、ものづくりにおける業務を一括管理するためのシステムです。企業に生産管理システムを導入すれば、製造業で行われているほとんどの業務を効率的に行うことができるようになります。
品質管理の手法には、簡単にできるものから複雑なものまで数多くあります。そして、各企業は1つだけの手法で品質管理を行っているわけでなく、いくつかの手法を組み合わせて行うことがほとんどです。
それらを手作業で行うには時間がかかり、人的コストも必要になります。そのような問題を解決するのが生産管理システムで、かなりの部分で自動化・業務効率化が図れます。特にデータ分析とグラフの自動化は、大きな時間の削減につながります。
また、生産管理システムで各データを一元化することによって、幅広いデータ分析が可能となり、品質管理の精度も増します。それに加え、誰でも・どこでも・いつでもデータを見ることができ、社員の品質管理に対する意識の向上と共有に役立ちます。
\気になる項目をクリックで詳細へジャンプ/
生産管理システムについて
生産管理システムの主な機能一覧
生産管理システムを導入する際、多岐にわたる機能の中から自社の業務に合わせた最適な機能を選択することが重要です。
機能 | 概要 |
---|---|
生産計画機能 | 予測や受注データを基に、最適な生産計画を立案 |
工程管理機能 | 各工程の進捗状況や工程間の連携を管理し、生産フローを最適化 |
販売管理機能 | 販売活動を一元管理し、顧客との取引履歴や売上を分析 |
在庫管理機能 | 製品や部材の在庫状況をリアルタイムで把握 |
発注・仕入管理機能 | 必要な部材や商品の発注、仕入れの管理 |
原価管理機能 | 製品の原価を計算 |
品質管理機能 | 製品の品質を一貫して管理し、不良品の発生を防ぐ |
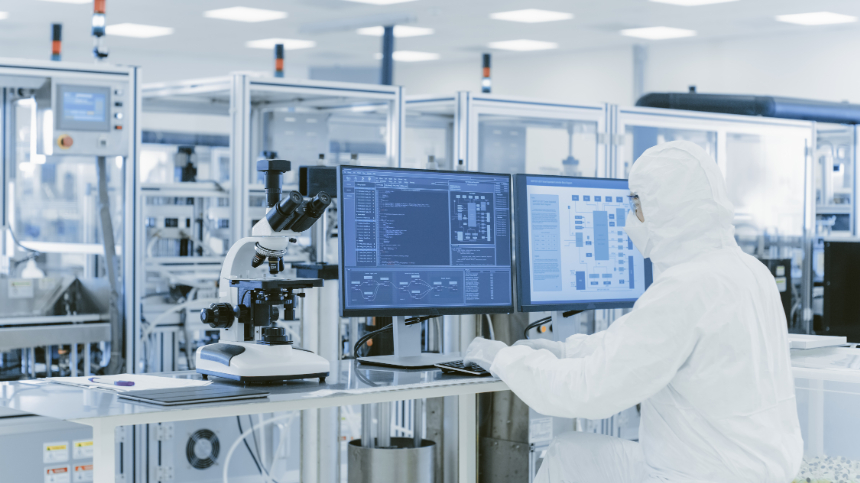
生産管理システムとは、生産・販売・原価など製造に関する情報を一元管理でき、課題を解決できるシステムです。業務の効率化や生産性の向上に期待でき、中小製造業でも導入している企業は多いです。本記事では、生産管理システムの主な機能やメリット、選び方のポイントを解説します。
生産管理システムを選ぶ際のポイント
生産管理システムには上述のような様々な機能があるため、まずは導入目的を明確にして、それに見合った機能が備わっているかを確認して選ぶことが重要です。また、自社の品質管理体制にスムーズに適用できるか、無料トライアルで確認するのがおすすめです。
ベンダーによるサポート体制も確認しておきたいポイントです。生産管理システムの導入により、業務フローには多少の変更が生じる可能性があります。特に多機能な製品の場合、使い方に迷うこともあるでしょう。導入・運用に際して手厚いサポートがあれば安心です。
まとめ

品質管理とは、製造した製品の品質を一定に保つように管理することで、基本業務は工程管理・品質検証・品質改善です。その手法はPDCAサイクル・QC7つ道具・IE・5S・4Mなど数多くあり、各企業が自社に合ったいくつかの手法を組み合わせて運用しています。
しかし、手法によっては手作業で行うには時間がかかり過ぎるものもあるため、生産管理システムを導入して効率的な品質管理を行う企業が増えてきています。
生産管理システムの導入は品質管理の効率化ばかりでなく、精度の高い品質管理や社員の意識の共有にも有効です。
この記事に興味を持った方におすすめ