生産管理における課題と解決方法|生産管理システムの選び方も解説
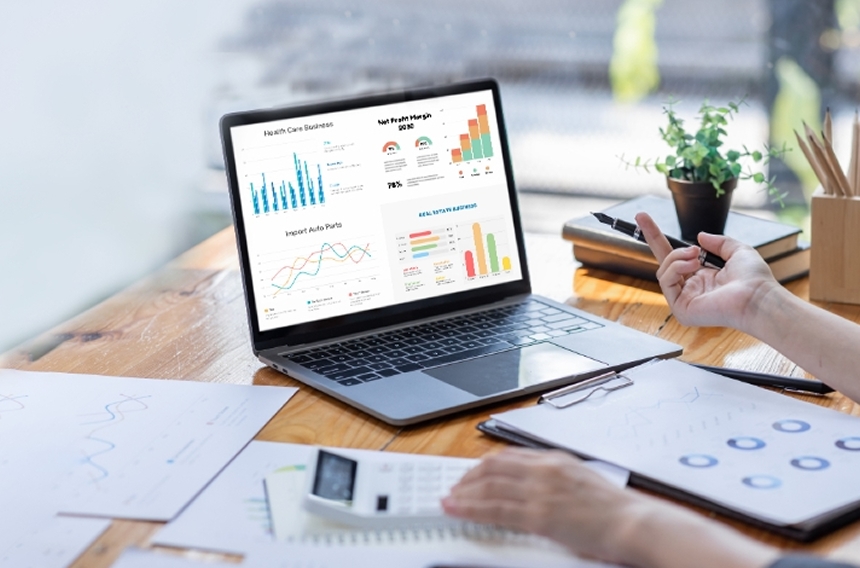
Check!
- 生産管理の課題には、特定の担当者への業務の属人化・原価管理の難しさなどがある
- 生産管理の課題解決方法としては、ノウハウの共有や生産管理システムの導入がある
- 生産管理システムを選ぶ際は、自社の課題を整理して導入目的を明確にすることが重要
生産管理とは、製品製造における材料の調達や製造工程を管理する業務全般のことを指します。しかし、生産管理においては、納期の遅れや過剰在庫といったさまざまな課題が発生します。本記事では、生産管理における課題と解決方法、生産管理システムについて解説します。
おすすめ記事
生産管理とは

生産管理とは、製造のためのプロセス全体を効率的かつ効果的に計画・調整・監視し、生産活動を最適化するための管理プロセスです。生産管理の出発点は製造計画であり、生産スケジューリングや材料調達、生産実行へと続きます。
そして、その他にも製品の品質管理や在庫・出庫管理などが生産管理に含まれ、プロセスは多岐にわたります。また、生産管理の目標は品質を維持しながらコストを最小限に抑え、生産効率を向上させて顧客の要求に迅速に対応することです。
ただし、多様な生産管理の工程において、納期の遅れや過剰在庫のほか、不良品の発生やヒューマンエラーの発生などの課題を抱える企業も少なくありません。
生産管理における課題

生産管理は、製品を生産する企業にとって不可欠なプロセスであり、効率的な製造のために重要です。ただし、その工程には多くの課題が伴います。これらの課題を認識・克服することは、競争力を維持して優良企業として存続するために重要なステップです。
ここからは生産管理の主な課題として挙げられる以下の7点について、詳しく解説します。
\気になる項目をクリックで詳細へジャンプ/
生産管理における課題
納期の遅れのリスクが高い
生産計画や需給予測が不正確なケースでは、需要に対する供給が充分に行われないことがあります。これにより、納期遅れのリスクが高まります。また、製品の材料や部品の供給が遅れる場合、生産が追い付かずに納期遅れが発生し、生産計画の最適化が難しくなります。
さらに、機械の故障やメンテナンスが原因で生産ラインが停止することがあり、納期遅れの原因になります。その他にも、熟練した作業員の不足や担当者のトレーニング不足により、生産効率が低下し、納期遅れを引き起こす可能性もあります。
納期遅れが発生すると、対応のために急な生産スケジュールの変更や早急な製造が必要になることがあり、コストを増加させることにもなります。そして、納期遅れにより取引先からの信頼性が低下し、将来のビジネスに影響を与える恐れがあります。
ヒューマンエラーが発生しやすい
作業環境が不適切である場合、ヒューマンエラーが発生しやすくなります。例えば、騒音や照明不足、労働スペースの不足などが注意力を分散させることでエラーが起こります。長時間の労働や不規則な勤務時間、過度の労働なども疲労を引き起こし、ミスにつながります。
ヒューマンエラーは製品の品質に影響を及ぼす可能性もあり、顧客満足度の低下や品質問題の増加につながることになります。また、エラーによって材料や時間、労力などの貴重なリソースが浪費され、コスト削減の目標を阻害するデメリットになります。
ヒューマンエラーを削減させるためには、トレーニングや作業環境の改善、プロセスの自動化、監視と品質管理の強化などさまざまなアプローチが必要です。また、エラーが発生した場合にはその原因を分析し、再発防止策を実施することが重要です。
過剰在庫や不良品で満足度が低下
需要変動を正確に予測することは難しく、需要予測の誤差が発生すると誤った予測が過剰な在庫を生み出す原因にもなります。また、生産計画が的確に作成されず、調整されていない場合には、生産量の過剰を生み出して過剰在庫となります。
品質管理が充分でない場合には、生産ラインによる製品に不良品が混入することになります。不良品は廃棄物となって廃棄コストなどが増加し、需給のバランスが崩れると過剰在庫となるケースも増え、品質の劣化などで不良品が発生することになります。
また、不良品が品質管理の過程などで見過ごされて出荷された場合、顧客満足度が低下し信頼性が損なわれます。これによって、企業の評価にも影響を及ぼすことになり、市場におけるビジネスチャンスや競争力低下にもつながります。
特定の設備・部門への負荷の偏り
生産プロセスや作業手順が標準化されていないと、それぞれの部門・設備ごとに、異なる方法で作業が行われることがあります。これにより、特定の設備などに過度の負荷が偏り、生産ライン全体に影響を及ぼします。
製造の負荷が特定の設備や部門に集中すると、生産ラインの遅延が発生しやすくなり、製品の納期遅れの原因にもなります。また、生産工程で過度の負荷がかかると、品質管理にも影響を与えて不良品の発生リスクが高まります。
特定部門への過度の負荷は、作業員のストレスや疲労を増加させ、モチベーションも低下し、生産効率の低減にもつながる可能性があります。ただし、生産ラインに標準化を導入することで、生産プロセスや作業手順が統一され、負荷集中などの状況を防げます。
部門・工場間で連携ができていない
自社の部門や工場で、異なる情報システムやデータベースを使用している場合、情報の共有や連携が難しくなります。また、それぞれの部門や工場は異なる業務目標や優先順位を持つことがあり、連携や共同作業が困難になります。
各部門間や工場間でのコミュニケーションが不十分であると、情報や課題の共有が滞り、誤解や意思疎通の問題を引き起こす可能性があります。さらに、個々の文化や業務プロセスにより、調整が難しくなって連携が阻害されることにもなります。
その他にも、部門や工場間の連携が充分でない場合には、情報共有が不十分となり、品質管理の面でも連携が取れないまま不良品が見逃され、顧客に不良品が出荷される可能性があります。このように、連携不足は市場での競争力低下を招くデメリットにもなります。
適切な原価管理ができていない
企業や組織における財務部門と生産部門は異なる役割と目標を持っています。財務部門が原価計算を行う際に、生産部門と充分な連携がとれていない場合には、正確な原価情報が得られず、適正な原価計算や管理が行われないことになります。
的確な原価管理が行われず、正確な原価情報が不足している場合、適正な製品価格の設定が難しくなり、利益率にも影響を及ぼします。また、生産戦略やコスト削減策なども効率的に実施できなくなるデメリットも発生します。
さらに、不正確な原価管理は企業の競争力の低下につながります。競合他社がコスト効率を向上させている市場においては、コストの正確な把握と管理は不可欠です。そのため、財務部門と生産部門の連携を強化し、正確なデータ収集と計算による原価管理が求められます。
担当者のスキル・経験に頼っている
生産ラインに人材不足が発生している場合には、特定の作業員のスキルや経験に頼って業務が集中し、業務の属人化が進行します。この場合、その作業員が退職や休暇を取った際には、業務の遅延や停滞が生じるリスクが高まります。
また、その作業担当者が組織を離れることによって知識やノウハウが組織から失われる可能性があり、長期的な競争力の低下につながります。また、業務集中によって作業員の負荷が増えて作業効率が低下し、納期遅れや品質低下にもつながります。
現在、人材不足の問題を抱えている場合は、組織全体でのスキルと知識の共有を促進し、トレーニングや教育プログラムを活用して新たな人材を育成することが必要です。また、業務プロセスの文書化や標準化、自動化の導入なども検討のポイントになります。
生産管理の課題を解決する方法

生産管理における課題は、企業の競争力や効率性に直接的な影響を及ぼします。しかし、これらの課題は克服可能であり、組織全体の協力と適切な戦略の導入によって効果的に対処できます。ここからは、その対処として以下の3項目について詳しく解説します。
\気になる項目をクリックで詳細へジャンプ/
生産管理の課題を解決する方法
工程管理シートの活用
工程管理シートは生産プロセスの各工程やタスクに関する情報を記録し、可視化するためのツールです。通常、工程名や担当者・予定日程・実績進捗・発生した問題点や課題などに関する情報が記述されます。
工程管理シートは生産プロセスを視覚的に表現し、作業の進捗状況を一目で把握できるため、生産プロセスを効果的に管理できます。また、予定日程と実績進捗を比較することで、スケジュールの把握や確認ができ、調整も容易に行えます。
工程管理シートには、発生した問題点や遅延などが記述されているため、問題が早期に発見でき、的確な対策を講じることができます。工程管理シートの導入と利用は、生産プロセスを効率的に運営して競争力を強化するために不可欠なツールとなります。
ノウハウを共有する
ノウハウの共有により、組織内の異なる部門やチーム間での知識とプロセスが統一され、標準化をする段階で役立ちます。これにより、生産プロセスの一貫性が維持され、品質管理の面でも効果があります。
ノウハウを共有することは、単一の作業員やチームに依存する属人化が避けられ、組織全体の知識ベースがより強固となり、リスクを分散できます。これにより、従業員の欠如や離職によって発生する影響が緩和され、課題解決にもつながります。
ノウハウの共有により、組織内の連携が強化され、異なる部門やチーム間で知識や情報を共有する習慣が築かれます。その結果、部門間のコミュニケーションが円滑に行われ、問題解決のアイデアも協力して出しやすくなります。
生産管理システムの導入
生産管理システムは、生産プロセス全体を統合的に管理し、効率性や品質を向上させるためのソフトウェアベースのツールです。一般的に、生産計画や在庫管理・品質管理・生産スケジューリング・モニタリング・分析とレポートなどの機能が搭載されています。
生産管理システムの導入により、生産プロセスの効率向上が図られ、生産管理の課題の1つである適切な生産効率の達成が可能となります。また、リアルタイムの品質監視と管理機能により、品質問題を迅速に解決して品質への課題を克服できます。
生産管理システムを利用するメリット

生産管理システムの利用によって、生産管理におけるいくつもの課題を解決することができます。ここでは、代表的なメリットを解説します。
\気になる項目をクリックで詳細へジャンプ/
生産管理システムを利用するメリット
ヒューマンエラーを削減できる
さまざまな製品に関わる、細かい材料・部品を取り扱う製造業において、人間では生産や発注のタイミングなどでミスを起こしやすいです。その点、生産管理システムを利用することで、発注ミスによる過重在庫・在庫不足といった問題を解消することができます。
その結果、生産計画の立案も正確に行うことができ、無駄なコストを発生させることなく、全体的な利益率の向上につながります。また、特定の管理部署や人材に対する負担の軽減にもつながります。
納期遅延のリスクを低減できる
生産管理システムを利用することにより、生産スケジュールの正確な管理が行え、出荷までの納期厳守によって、納期遅延のリスクが低減されます。さらに、原価管理や在庫管理機能の活用により、適切な原価から抽出した在庫のみを保有し、余分なコストが削減できます。
また、部門間の連携が強化され、生産工程の課題に協力して対処することも可能です。
生産管理システムを選ぶ際のポイント

適切な生産管理システムを選ぶことは、組織の生産プロセスと効率性向上において重要なステップとなります。システムの選択においては、組織のニーズや目標を十分に理解し、以下の4項目をポイントに検討することが大事です。
\気になる項目をクリックで詳細へジャンプ/
生産管理システムを選ぶ際のポイント
導入目的を明確にする
生産管理システムを選ぶ際の重要なポイントの1つが、導入目的を明確にすることです。導入目的を明確にすることにより、組織の具体的な要件とニーズを特定することができ、どのような課題を解決し、達成したい目標を社内全体で理解することができます。
目的が明確な場合は、それに合致する機能を持つ的確な生産管理システムを選択でき、無駄なコストを抑えることができます。導入目的の明確化はプロジェクトの方向性や目標が従業員にも正確に伝わり、プロジェクト成功に向けた共通の認識を持つことができます。
また、目的を明確にすることにより、システムの導入後に目的の達成度を評価しやすくなります。成功の基準を持つことはプロジェクトの進行状況を評価し、必要に応じて調整するために不可欠です。
導入形態を確認
生産管理システムの導入形態には、クラウド型とオンプレミス型の2つの選択肢があります。どちらを選択するかは、組織のニーズと状況に合わせて検討する必要があります。ここでは、それぞれの特徴などを解説します。
クラウド型
クラウド型のシステムは、データやアプリをインターネット上のサーバーに保存し、ユーザーはブラウザや専用のアプリを使用してアクセスします。この形態では、サーバーなどの必要なリソースをプロバイダーが提供し、ユーザーは必要に応じてリソースを利用します。
メリットとしては、機器の設置や保守にかかるコストを削減でき、初期投資などのコストが低減できます。また、インターネットを介したアクセスにより、場所やデバイスに依存せずにリモートからでも利用でき、柔軟性のあるシステム稼働が可能となります。
対してデメリットとしては、稼動をプロバイダーに依存することになり、サービス提供者が停止・変更する場合に影響を受ける可能性があります。そして、セキュリティへの対応や大量のデータ転送を行う場合には、回線スピードの制約により遅延が生じることもあります。
オンプレミス型
オンプレミス型システムは、自社のセンターにサーバーなどのハードウェアを設置し、そこに生産管理ソフトウェアやアプリを導入して、組織内でシステムを運用・管理する形態となります。
メリットとしては、自社でデータとシステム全体の完全なコントロールを持ち、セキュリティとプライバシーを維持できます。また、特定の要件に合わせてカスタマイズしやすく、調整や拡張ができます。通信遅延が少なく、高速で処理や応答できる可能性があります。
デメリットとしては、ハードウェアやソフトウェアの購入、システムの導入や構築、運用や保守用のスタッフなど、初期コストと運用コストが高額になる傾向があります。システムの保守や更新などは自社内で実施することになり、時間とリソースを要します。
自社の生産方式に合っているか
生産管理システムを選ぶ際のポイントとして、自社の生産プロセスに合致するかどうかの確認が非常に重要です。自社の生産方式にマッチしたシステムは、導入がスムーズで教育や運用が迅速に実施でき短期間でのシステムの導入や活用が可能となります。
また、生産プロセスに関する課題や特定の問題に対する効果的な解決策を迅速に適用できます。自社の成長に合わせて生産方式が変化する場合にも、適応性があることによって将来のニーズにも対応しやすくなります。
サポート体制が充実しているか
生産管理システムを選ぶ際には、サポート範囲の確認も大事です。システムの導入において支援を行ってくれるかどうかを確認しましょう。具体的には、システムの設定・カスタマイズ・トレーニング・データ移行などです。
そして、システム導入後のサポート内容もチェックしましょう。バグ修正やアップデート、機能拡張などのサポート範囲を確認します。また、自社のカスタマイズや新機能の開発をサポートしてもらえるかも確認ポイントになります。
その他にも、問い合わせ方法として、電話やメール、チャットなど組織のニーズに合致しているかどうかも検討するのがおすすめです。サポート時間として、平日・休日・緊急時など24時間のサポートが提供されているかどうかの確認を行いましょう。
まとめ

生産管理にはさまざまな課題が存在します。主に、納期遅れや過剰在庫、不良品の発生といった課題が挙げられ、ヒューマンエラーや部門間の連携不足、原価管理の難しさや担当者のスキルに頼る傾向も生産管理の課題です。
これらの課題を解決するためには、適切な生産管理システムの導入やプロセス改善、スキル向上トレーニングなどが必要です。また、生産方式に合ったシステム選定や導入後のサポートの充実も大切です。
課題への対応として生産管理システムを選ぶ際には、導入の目的を明確にして自社の要件に合致する機能を持つ的確なシステムを選択して導入しましょう。
この記事に興味を持った方におすすめ