ロット管理とは|ロット管理に在庫管理システムがおすすめな理由
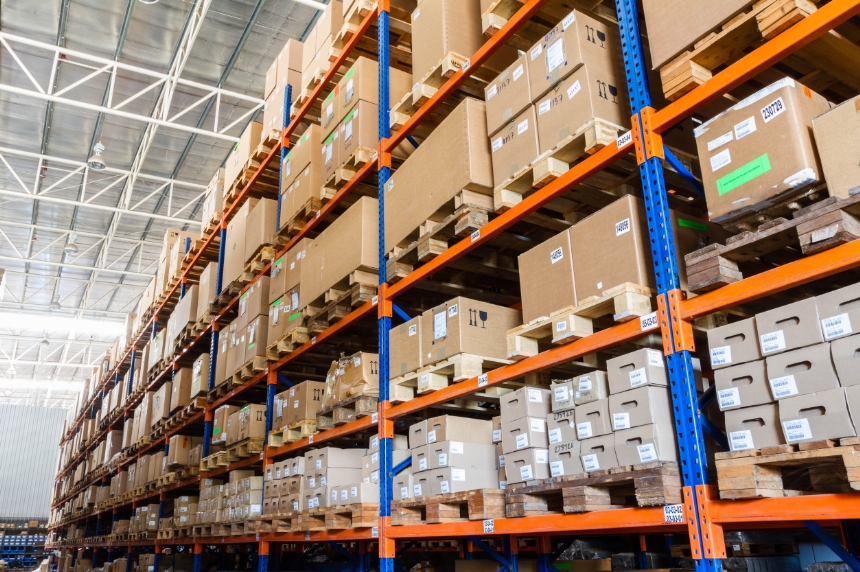
Check!
- ロット管理とは、ロット番号を製品ごとに割り当て、商品を管理することである
- ロット管理を行うことで、在庫管理を効率化でき、ロスやコスト削減にもつながる
- ロット管理の課題解決には、在庫管理システムの利用がおすすめである
在庫管理でロット管理をすることには、複数のメリットがあります。効果的なロット管理の課題解決には、在庫管理システムの利用がおすすめです。本記事では、ロット管理とシリアル管理との違い、ロット管理に欠かせないトレーサビリティについてなどについて解説します。
おすすめ記事
目次
開く
閉じる
開く
閉じる
ロット管理とは

ロット管理とは、同一条件で製造される製品の製造および出荷数量の最小単位である「ロット」を使用し、製品ごとにロット番号を割り当てて製品管理をしていく方法です。
ロット管理では、原材料の調達から製造・出荷・流通・販売に至るまでの工程を管理でき、製品がいつ・どこで・誰が・どうしたのかを適切に把握可能です。
また、消費期限切れや品質不良の商品が発生した場合も、ロット管理をしておくことでどの商品が回収の対象になるのかを突き止めやすく、迅速に適切な処置を行うことができます。
ロットとは
ロットとは、ある製品を同一条件下で製造・出荷する場合における製造数量および出荷数量の最小単位のことです。主に製造業で使われる言葉ですが、最近では物流業界でも使用されています。
1ロットの個数については決まりがなく、製造側が製品や部品の状況に応じて独自に設定します。そのため、1ロットといっても、10個または100個だったりとまちまちです。ただし、同一条件で生産されたものは、基本的に同一ロットになります。
製造ロット
製造現場では現在の需要や受注量などを見ながら、製造ラインでの生産量を算出します。この際に算出した製造量の最小単位が製造ロットです。製造ロットに基づいて、生産量を調整しています。
同じ製造ロットの場合、すべて同一条件で製造されたということになります。そのため、不良品が出た場合も、同じロット番号を探すことで不良品の特定が迅速かつ容易にできます。
特に、大量生産を行う企業では多くの在庫を抱えがちです。製造ロットを規定することで需要に見合った生産が可能となり、在庫過多を防止することで製造での原材料費や人件費・光熱費などの無駄なコストも削減できます。
購入ロット
購入ロットは受注ロットまたは注文ロットとも呼ばれ、製品を取引先へ販売する際に指定する販売数のことを指します。
製品が販売されるまでには、製品自体のコストのほかに保管や輸送など多くの流通コストが発生します。そのコストを回収するために、ある程度の数量をまとめて販売する必要があります。
購入ロットは、製造者側が決めることが多いです。しかし、ロットを小さくして単価を上げたり逆にロットを大きくして単価を下げたりするなど、製造者側と購入者側の交渉で調整することがよくあります。
最小ロット
最小ロットは、生産性とコストの面から産出された1度に生産できる数量や重量の最小単位で、「ミニマム」または「ミニマム・ロット」と呼ばれています。生産や輸送などすべての工程で発生するコストを考慮し、損失にならない範囲で設定されます。
最小ロットは、「製造」および「販売」ができる最低限の数量です。この最小ロットは製造者側が設定します。例えば、製造者が最小ロット30個と設定している場合、購入者は30個以上でないと注文できません。
最小ロットは購入者側にとっても重要です。大量に仕入れると不良在庫を抱えるリスクがあるため、多くの業者はまず最小ロットで仕入れて販売し、販売状況を見てから追加を発注する形式を採っています。
シリアル番号管理との違い
ロット管理とは別の製品管理の方法に、シリアル番号管理があります。シリアル番号管理は製品や部品ごとにシリアル番号を付与し、それぞれ管理する方法です。
ロット管理が製品・部品をいくつかまとめた「ロット」をもとに管理を行うのに対し、シリアル番号管理は製品・部品を個別に管理しているという違いがあります。
そのため、製品に問題が発生した場合、問題がある個体そのものを特定できます。一方、ロット管理は同一ロットの製品はすべて同じ識別番号になり、ロット内のどの個体かを特定できません。
ロット管理に欠かせないトレーサビリティとは

トレーサビリティ(traceability)とは、原料の調達から生産、消費又は廃棄までのサプライチェーンにおいて、各工程を追跡可能な状態にすることです。追跡(trace)と能力(ability)の合成語で、日本語では「追跡可能性」「生産履歴」などを意味します。
近年では企業も消費者や行政の要望に応じ、トレーサビリティの構築に取り組んでいます。
ロット管理をしていると、ロット番号でいつ・どこで・誰が・どのように製造・保管して出荷されたかがすぐに判明します。
そのため、製品に問題があった場合もロット番号があると回収などの対応が取りやすくなります。また、どの工程に何の不備があったのかを追跡する際にも、該当ロット番号の状況を調査すれば原因を見つけやすくなります。
トレーサビリティの2つの種類
トレーサビリティには「チェーントレーサビリティ」と「内部トレーサビリティ」という2つの種類があります。どちらのトレーサビリティも、企業活動において重要な要素となっています。
チェーントレーサビリティは、原材料の生産から製造、小売業者など企業をまたいで情報を追跡する手法です。食品業界では食品の原材料から製造、流通、小売までの過程を追跡し、製品の安全性や品質を保証しています。
一方の内部トレーサビリティは、1つの工場や企業内で製品の製造や検証の過程を追跡する手法です。例えば、製造業において部品の問題が発生した場合、その部品を使用している製品情報を把握し、不良品の流通を防ぐことが可能になります。
ロット管理のメリット

ロット管理によって製品の原料調達から販売までを管理できるようになることで、さまざまなメリットを得られます。ここでは、ロット管理を行うことのメリットについて解説します。
\気になる項目をクリックで詳細へジャンプ/
ロット管理のメリット
在庫管理を効率化できる
ロットごとに決められた番号を付与しておくと、その番号のロットに入る製品に対して製造日や入荷・出荷日などの情報を紐付けられます。
原則、同じロットで管理されている製品は、どれも同じ製品です。そのため、1ロットの数が非常に多くても、製品の状態や消費期限といった情報を把握する際は製品1つを確認するだけで済み、在庫管理を効率的かつ適切に進められます。
また、製造日などの情報を紐付けしていることで、製品に消費期限や有効期限がある場合は古いものから順番に出荷でき、期限切れによる廃棄の無駄が減少します。
ロスやコストを削減できる
商品は時期によって購入量に変化があります。この需要の予測を間違うと、過剰在庫を抱えかねません。しかし、製品に関する情報をロットごとに管理していると、時期によって製品の必要量の推移がわかりやすくなります。
ロット単位で製造や入出荷をコントロールできるため、需要供給の状況に応じた計画を立てられます。過剰在庫を生むことがなくなれば保管費用の削減が可能です。また、最小ロットを設定すると、コストに見合わない無駄な生産を行うことを防げます。
不良品の特定・追跡が行いやすくなる
ロット管理を行っていると、ロット番号を確認すればその製品がいつ・どこで・誰が・どう作られたかの情報を確認できます。そのため、製品の原材料調達から製造・出荷、販売に至るまでの工程を一元管理することが可能です。
もし、消費者などから不良品の連絡があった場合、製品に印字されたロット番号で該当ロットがわかります。同じロットの製品は、同じく不良品である可能性が高くなります。
ロットが一元管理されていると、該当ロットがどこへ行ったのかすぐに特定できます。不良品を迅速に追跡できるため、トラブルや被害が大きくなる前に製品の回収を行いやすくなります。
ロット管理の注意点

ロット管理を行うことで得られるメリットは多いですが、いくつかの注意点を把握しておくことも大切です。ここでは、ロット管理の注意点について解説します。
\気になる項目をクリックで詳細へジャンプ/
ロットに関するルールを定める
ロット管理は、製造年月日や原料などあらゆる情報をデータとして管理しなければならないため、管理に関わる全従業員が共通の認識を持って管理を行う必要があります。
特に、種類ごとに1ロットあたりの個数は異なることから、ロットではなく製品自体の個数に関するルールを設定し、全員が同じ認識で管理できるよう説明や周知を行いましょう。煩雑な在庫管理では、正確な在庫管理ができなくなります。
顧客目線での最小ロット設定が必要
最小ロットは製造者によって自由に設定できますが、顧客目線での設定を心掛けることが大切です。ライフスタイルや働き方が大きく変わりつつある現代では、販売スタイルも変化しています。
ECの浸透が進み、従来よりも小ロットの需要が高まっています。生産スピードが早い場合は大きなロットとなりやすいため、顧客ニーズを捉えた適切なロット設定を行いましょう。
トレーサビリティを確保しておく
製造・流通においては、トラブルや異常が発生した際に影響範囲の特定と早期対応が必要になります。そこで、トレーサビリティを確保しておくと、異物混入が発生した該当のロットや、不良品の影響を受けた部品を迅速に追跡・特製することが可能です。
トレーサビリティの確保には、製造日・製造ライン・使用した原材料など、生産工程の記録を行い、ロット番号ごとに追跡できるようにしておきます。また、在庫管理システムを活用すれば、ロットの追跡を正確かつ効率的に行うことが可能です。
賞味期限・消費期限を適切に管理する
食品、医薬品、化粧品などの分野では、消費者や使用者の安全性を守るために適切な期限管理が求められます。仮に、賞味期限や消費期限を超えた製品を出荷してしまった場合、品質低下や安全性の問題が発生する恐れがあるため、厳重な注意が必要です。
特に、ロットの中で1つでも期限切れが発生した場合には、すべての製品を回収しなければならず、廃棄リスクの増加によって大きな損失にもつながります。賞味期限・消費期限は適切に管理しつつ、廃棄ロスやトラブル防止に努めることが大切です。
ロット管理が適しているアイテム

ロット管理は品質保証やトレーサビリティの観点から、消費期限が設定されている商品においては欠かせない手法です。具体的には、食品や医薬品、化粧品などが該当します。ロット管理により期限切れを避け、品質を維持できます。
また、電子部品や自動車部品などでもロット管理が行われています。例えば、自動車メーカーでは、エンジン部品やブレーキパッドなどの各部品ごとにロット番号を割り振っています。
不具合が発生した場合、該当ロットを特定して迅速に対応し、信頼性の高い商品を提供することが可能になります。
ロット管理の方法

ロット管理の方法には、エクセルで管理する方法と在庫管理システムを使う方法の2つがあります。ここでは、2つのロット管理の方法について解説します。
\気になる項目をクリックで詳細へジャンプ/
ロット管理の方法
エクセルで管理する
同一条件で生産した製品群にロット番号を振り、ロット内の製品に番号を付けることでロット管理を行う方法です。製品にロット番号を付けるには、機械による印字に加え、回転式ゴムスタンプ、シールの貼付が挙げられます。
同一ロットごとに保管し、ロット番号それぞれの製品情報をエクセルに入力しながら管理を行います。この方法の場合、企業ならすでに所持しているモノを用いることから、導入が簡単で費用も少なくて済みます。
しかし、ロット番号と製品情報を人間が管理するため、入力担当者の負担が増えてミスも起きやすいです。対策としては、在庫管理表のレイアウトを入力しやすいものにしたり、関数やマクロを組み込んで半自動化したりするのがおすすめです。
在庫管理システムを導入する
在庫管理システムとは、在庫の入荷から移動・出荷に至るまでの情報を一元管理するためのシステムです。在庫状況の一元管理をはじめ、入出庫や返品の管理などの機能が搭載されています。
また、ハンディターミナルなどの端末を使って検品や棚卸チェックができる機能もあります。システムとロット番号を紐付けておくと端末を使ってロット番号を読み取れるため、製品情報を入力する手間が省けます。
その他、入出庫の際にロット番号を読み込むと入出庫の情報がリアルタイムで記録されます。出荷の先入れ・先出しを徹底し、消費期限切れの廃棄といった無駄を減らせるだけでなく、不良品が発生した際も所在が明確で回収しやすくなります。
ロット管理に在庫管理システムがおすすめな理由

在庫管理システムは入出庫する製品の情報を一元管理し、ロット番号を紐づけて管理することが可能です。
印字されたロット番号を記載したバーコードを、ハンディターミナルなどの端末で読み取り、数量とともにシステムに登録しておきます。この作業をしておくと、後でバーコードを読み取るだけでロット番号や製品情報はもちろん、残量も自動的に把握できます。
ロット番号をシステムでリアルタイムに管理できることで、取引先などからの問い合わせにも迅速な対応が可能です。万が一不良品が出て回収する場合も、情報が把握できているため被害を少なく抑えられるでしょう。
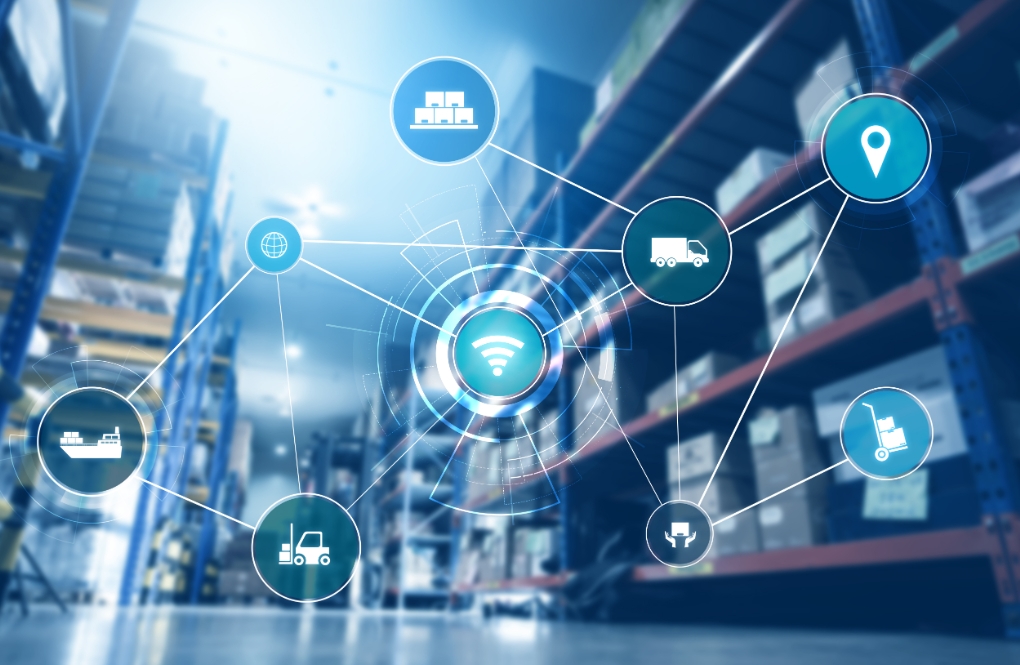
おすすめの在庫管理システム8選|選び方や導入手順を詳しく解説
在庫管理システムは、在庫の情報を効率的に管理し、正確な在庫状況を把握することができるツールです。システムの導入をしたくても種類が多くてどれを選べば良いか分からない企業もあるでしょう。本記事では、おすすめの在庫管理システムと選び方を解説しています。
まとめ

ロットとは、ある製品を同一条件下で製造・出荷した場合の、製造・出荷数量の最小単位のことです。ロットには製造で必要な「製造ロット」、販売の際に使われる「販売ロット」、1回の生産における最小単位「最小ロット」などがあります。
これらのロットを管理することで、製品の原材料調達から販売までの工程を把握できます。ロット管理を適切に行うと、近年重要視されているトレーサビリティの構築に役立ち、不良品が出た際も回収などの対応が取りやすくなります。
ロット管理には、エクセルを使う方法と在庫管理システムを使う方法がありますが、エクセルでは入力に手間がかかり人的ミスが増えることが短所です。在庫管理システムの場合、搭載機能で入力を自動化し、ミスも削減できるためおすすめです。
この記事に興味を持った方におすすめ