生産管理とは?工程管理との違いや仕事内容、よくある課題も解説
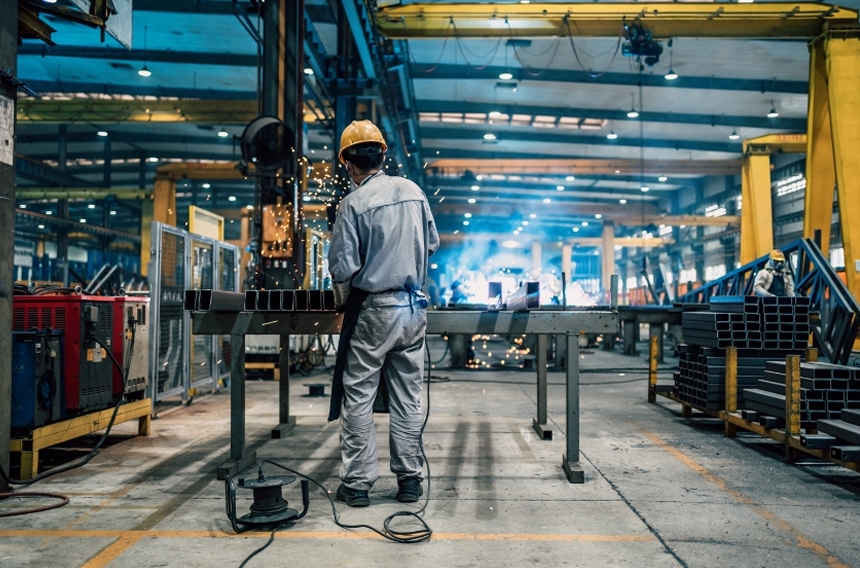
Check!
- 生産管理とは、生産の計画や在庫・品質・進捗の管理など製造工程における管理業務全般
- 生産管理の具体的な仕事内容として、需要予測・生産計画・在庫管理・品質管理等がある
- 生産管理の現場では、業務の属人化や進捗把握が難しいことなどが課題となっている
生産管理とは、生産の計画や在庫・品質・進捗の管理、材料の調達など製造工程における管理業務全般を指します。生産管理の目的は、QCDの最適化です。この記事では、生産管理の基本的な仕事内容やよくある課題などについてわかりやすく解説します。
おすすめ記事
生産管理とは

生産管理は、製造業において製品の生産プロセスを計画・調整し、効率的に遂行するためのアプローチです。生産計画の策定や材料の調達、工程のスケジュール管理、品質管理、在庫管理、納期管理など、幅広い業務をわかりやすく包括的に管理します。
また、生産管理は単なる工場の操作にとどまりません。部門間の連携や情報共有が不可欠であり、営業・調達・製造・物流などの部門が連携して、全体の調和を図ります。製造業は常に競争が激化しており、生産管理は企業の競争力を高める重要な要素となっています。
工程管理との違い
工程管理は、プロジェクト内で特定の工程やタスクを計画・スケジュール・監視し、効果的な進行を確保するプロセスです。生産管理の一部であり、プロジェクト内の特定の工程の進行を最適化する役割を果たします。
一方、生産管理は、資材調達・品質管理・在庫管理などの製造全体を管理し、効率的な生産を確保することが役割です。工程管理はプロジェクト固有の側面に焦点を当て、生産管理は製造全体の最適化に役立ちます。
生産管理の目的

生産管理の主要な目的は、「品質(Quality)」「コスト(Cost)」「納期(Delivery)」の頭文字を取ったQCDの最適化です。品質の最適化は、不良品や欠陥の発生を最小限に抑え、製品やサービスの品質を向上させることを意味します。
コストの最適化は、生産プロセスや資材の効率的な利用に焦点を当て、生産コストを削減し、企業の収益性を向上させます。納期の最適化は、顧客への製品やサービスの提供を迅速かつ正確に行い、市場競争力を維持します。
生産管理は企業の競争力を高め、市場で成功を収めるために、QCDをバランスよく最適化します。持続可能な成長、顧客満足度の向上、競争優位性の獲得など、企業の長期的な目標達成に効果的です。
生産管理の基本的な仕事内容

生産管理には多くの業務が含まれ、効果的な生産活動を支えます。また、これらの業務を統合し、組織全体の生産活動を効率的かつ効果的に管理します。ここでは、生産管理の基本的な仕事内容について解説します。
\気になる項目をクリックで詳細へジャンプ/
需要予測
需要予測は、市場や顧客の需要を事前に予測する作業です。この業務では、過去の売上データや市場動向、競合情報、季節性などの要因を分析し、将来の需要を予測します。
予測された需要情報は生産計画に重要な役割を果たし、どの製品をいつ、どれだけ生産すべきかを決定する際に参考にします。需要予測によって、在庫の最適化、材料の調達計画、生産スケジュールの立案など、生産活動全般を戦略的に計画するための基礎が提供されます。
生産計画
生産計画は、顧客からの受注、市場の需要予測、在庫レベル、製品の生産能力などを考慮に入れて、どの製品をいつ、どれだけ生産すべきかを決定します。
在庫を最小限に抑えつつ、顧客の納期要求を満たし、効率的な生産を実現します。正確な生産計画は、製品供給の安定性、生産効率の最適化、コストの最小化に貢献し、企業の競争力を向上させます。
工程計画
工程計画は、製品の製造工程や工程の順序を決定し、各工程のスケジュールを策定します。具体的には、製品の仕様に基づいてどの工程をどの順序で実行するかを計画し、必要な材料や資源を確保します。
また、作業者の配置や製造設備の稼働計画も工程計画の一部です。生産プロセスを最適化し、製品の生産を効率的かつ高い品質で行います。
工程計画によって、リードタイムの短縮、生産コストの削減、品質の確保が実現され、競争力を維持・向上させることが可能です。工程計画は製造業における生産活動の中心的な要素であり、生産計画や生産スケジュールの基盤となります。
調達・購買
調達・購買は、材料の選定、供給業者との契約交渉、価格交渉、納期の調整、在庫管理、品質管理などを行います。生産計画と協力して、必要な材料が生産現場に適切なタイミングで供給されるようにスケジュールします。
また、適切な供給業者との協力により、コスト削減や品質向上の機会を追求し、企業の競争力を強化することが可能です。調達・購買の効果的な運営によって、生産プロセスの中断や遅延を防ぎ、スムーズな生産活動を実現する役割を果たします。
在庫管理
在庫管理は、適切な在庫レベルを維持し、生産のスムーズな遂行を確保します。具体的には、在庫の受け入れ、格納、出庫、再注文、廃棄などを行います。
在庫は生産の中断や納期遅延を防ぐために必要ですが、過剰在庫はコストを引き上げる可能性があるため、バランスが求められます。
在庫管理では、需要予測や生産計画と連動し、必要な在庫レベルを決定します。また、品質管理や備蓄対策も考慮し、品質の維持とリスクの軽減を目指します。
品質管理
品質管理は製品やプロセスの品質を監視・評価・確保するために行われます。業務内容としては、製品の品質基準の設定、品質検査の実施、不良品の取り扱い、品質データの収集と分析、品質改善活動などです。
品質管理は、顧客に高品質な製品を提供し、不良品を最小限に抑えることを目指します。製品の信頼性と安全性を確保し、リコールやクレームのリスクを軽減します。
また、品質データを分析し、生産プロセスの改善に貢献する役割も果たします。品質管理は製品の品質基準を厳守し、企業の競争力を維持するために重要な業務です。
進捗管理
進捗管理では、各工程やタスクの進捗を定期的に監視し、計画通りに進行しているか確認します。スケジュールの調整、リソースの配分、問題の特定、対策の立案、チームや部門とのコミュニケーションなどの業務があります。
目的は、プロジェクトや生産プロセスを効率的に遂行し、納期を守り、コストを最小限に抑えることです。また、進捗管理はリスクを早期に識別し、適切なアクションを実施して問題を解決する役割も果たします。
原価管理
原価管理は、製造過程における労働・材料・輸送・設備のコストを追跡し、予算と実際のコストを比較してコスト効率を確保します。原価管理には、原価計算、予算策定、コスト削減策の検討、コスト分析、価格設定などが含まれます。
目的は、生産プロセスのコストを最小化し、利益を最大化することであり、競争力を維持・向上させます。また、原価管理は経営戦略にも影響を与え、製品価格の決定や新製品の開発において重要な情報を提供します。
生産管理における課題

生産管理の現場ではさまざまな課題が発生し、効率的な生産活動を妨げることがあります。これらの課題に対処することは、企業の競争力向上に不可欠です。ここでは、生産管理における課題について解説します。
\気になる項目をクリックで詳細へジャンプ/
生産管理における課題
進捗・トラブルを把握しづらい
製造業において、日報や作業記録の手作業入力は一般的であり、リアルタイムな進捗状況の把握が困難です。手入力には人為的なエラーや遅延のリスクが伴い、生産プロセスの正確なトラッキングが難しくなります。
これによりトラブルの発見が遅れ、納期遅延や品質問題、クレームに繋がる原因となります。リアルタイムで進捗を把握できないため、問題が発生した時点で対処が遅れ、コスト増加や顧客満足度の低下に繋がる可能性が高まります。
業務負荷が偏っている
課題の一つとして、業務が特定のスキルを持つ従業員に依存し、その業務が属人化してしまうことがあります。この状況では、特定の従業員が不在の際や退職時に問題が生じ、知識やスキルの共有が不足します。
また、一部の部門や工程に業務負荷が偏り、他の部門や工程が余剰のリソースを抱えることがあります。これにより、効率性が低下し、リソースの無駄遣いが発生します。
部門間の連携が不足することで、生産プロセス全体の最適化が妨げられ、納期遅延やコスト増加といった問題が生じてしまいます。
情報共有ができていない
各部門が独自に情報を管理し、データやレポートが散在していると、情報の一元化が困難になります。これが生産プロセス全体の透明性を損ね、意思決定の遅延や誤った判断を招くことがあります。
また、情報の不一致や更新の遅れが品質問題や納期遅延に繋がる可能性も高まります。さらに、生産計画や在庫管理、品質管理などの業務が連動していないため、最適な生産スケジュールの策定やトラブルの早期発見が難しくなります。
原価を正確に把握できていない
製造過程では、原材料の価格変動や生産条件の変化などが頻繁に発生し、これが正確な原価計算を難しくします。原価の変動が把握できないと、製品の価格設定や収益計画に誤差が生じ、利益率やコスト効率の見積もりが不確かになります。
さらに、誤った原価情報に基づいて製品を生産することがあれば、赤字を生む可能性が高まります。
生産管理を効率化する方法

生産管理を効率化するためには、生産管理システムを導入することをはじめとしたいくつかの方法があります。ここでは、企業の業務改善や生産プロセスの最適化に繋がる方法を3つ解説します。
\気になる項目をクリックで詳細へジャンプ/
生産管理を効率化する方法
生産管理システムを導入する
生産管理システムは、製造業における生産プロセスを効率的に管理するためのソフトウェアツールです。このシステムは、生産計画・在庫管理・品質管理・リソース管理などの業務を一元管理し、リアルタイムでデータを収集・分析する機能を提供します。
生産管理システムの導入により、情報の一元管理が実現され、各部門や工程のデータが統合されます。これにより、生産プロセス全体の透明性が向上し、情報共有が円滑になります。
また、製造過程での原価変動や進捗状況が迅速に把握でき、正確な原価計算や進捗管理が実現可能です。さらに、生産管理システムは品質管理にも貢献し、品質情報の収集と分析をサポートします。
このように、生産管理システムの導入には情報の一元化、透明性の向上、リアルタイムデータの利用、品質管理の強化などが含まれ、生産管理の課題解決と競争力の向上に大きく貢献します。
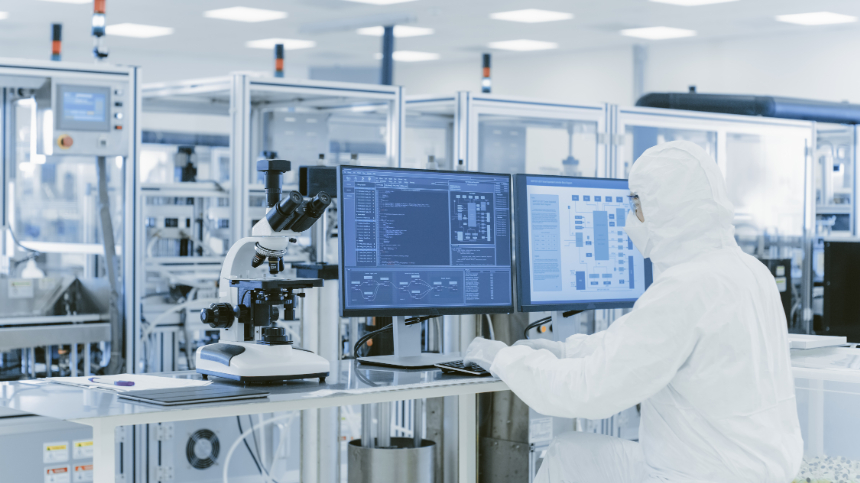
生産管理システムとは、生産・販売・原価など製造に関する情報を一元管理でき、課題を解決できるシステムです。業務の効率化や生産性の向上に期待でき、中小製造業でも導入している企業は多いです。本記事では、生産管理システムの主な機能やメリット、選び方のポイントを解説します。
業務属人化を防止する
業務属人化とは、特定の業務が担当者に依存している状態です。生産管理業務のプロセスにおいても、多くの部門・人員が関わることや、複数の管理方法が併用されていることなどにより、業務が煩雑になり、一部で属人化しているケースが見られます。
業務が属人化すると担当者の不在や退職で、業務が滞ったり遂行できなくなったりする可能性があるため、生産管理プロセスを効率化するためには、まず属人化を予防・解消することが重要です。
属人化の予防には、業務のマニュアル化や標準化が有効な手段となります。業務を可視化してマニュアルを作成し、多くの社員が一定の品質・スピードで業務を遂行できる環境を整えることが、属人化の予防・解消に繋がります。
PDCAサイクルを意識する
PDCAサイクルとは、「Plan(計画)・Do(実行)・Check(確認)・Action(改善)」の頭文字を取った用語で、業務改善のためのフレームワークを意味します。生産管理業務においても、PDCAサイクルを意識することは重要です。
特に、「Check(確認)」「Action(改善)」のプロセスが重要となります。目標達成の可否についてその結果に至った理由を分析し、目標達成出来なかった場合には、課題や改善点を見つけてPDCAサイクルを繰り返すことで、生産管理プロセスの最適化が実現します。
【PDCAサイクルの手順】
- 生産管理の目標を立てる
- 目標達成のための行動を実行する
- 得られた成果を確認・分析し、課題や改善点を見い出す
- 改善策を実施する
- 1~4の流れを繰り返す
まとめ

生産管理は、生産プロセスの効率化を図り、企業の競争力向上に貢献します。しかし、従来の手動プロセスでは進捗やトラブルの把握が難しく、業務負荷の偏り、情報共有不足、原価の正確な把握といった課題が生じていました。
こうした課題の解決には、生産管理システムの導入がおすすめです。システムは、生産プロセス全体を一元管理し、リアルタイムでデータを収集・分析できるため、進捗やトラブルを把握しやすく、業務負荷の均等分散が可能です。
また、情報の一元化と共有が実現され、部門間の連携がスムーズになり、原価計算の正確性が向上します。急速に変化する市場に対応するためにも、生産管理システムの導入を検討しましょう。
製造業は激しい競争の中で生き残るために、生産管理システムの導入を真剣に検討すべきです。これは、現場の課題克服と将来の成長に向けた重要な投資です。
この記事に興味を持った方におすすめ